Sacmi signs the new Bäherden Ceramics factory in Turkmenistan
The most modern and important ceramic plant in Turkmenistan was inaugurated on 12th March and will produce both tiles and sanitaryware.
A grand inauguration for Bäherden Ceramics in Turkmenistan: located near the capital, Ashgabat, this all-greenfield, Sacmi-built factory will produce both tiles and sanitaryware.
The official ceremony was held on 12th March in the presence of the President of the Republic of Turkmenistan, Serdar Gurbangulyýewiç Berdimuhamedow, the Prime Minister, the Minister of Industry and Economic Development and other high-ranking local officials.
This project had a clear ambition: to create an ultra-modern, highly productive plant capable of making a major contribution to the national output of high-quality tiles and sanitaryware. Hence the decision to join forces with Sacmi which once again confirms its unique ability to manage highly ambitious projects anywhere in world, skillfully, effectively and with guaranteed results.
The ceramic tile plant
On the tiles side, the plant features a body preparation department - containing everything from raw material batching systems to mills, spray dryers and storage silos - that feeds two separate production lines, one mainly producing monoporosa wall tiles, the other single-fire wall and floor tiles. Total output reaches about 8,500 m² per day per line, depending on product size and thickness.
Size-wise, the focus will be on the market’s most popular formats, from 30x60 to 60x60 cm. However, the plant can also produce slabs as large as 80x160 cm thanks to the four Sacmi presses (two PH3500s and two PH6500s). After forming, the two lines converge on the drying, glazing and digital decoration (DHD 1208) machines. The tiles are then conveyed to the firing department, which features two FMS kilns, complete with pre-dryer, having an overall length of about 160 meters.
Completing the tiles plant are the polishing and grinding lines supplied by BMR. Sacmi also provided the packaging and sorting department. Handling is managed by automatic LGVs (laser guided vehicles) and includes on-truck loading of the already-packaged products stored in the buffer that connects the Tiles and Sanitaryware production areas.
The sanitaryware plant
Sacmi has designed a 200,000-piece-per-year plant for Bäherden Ceramics, with an on-site plaster mold production department. Casting may be manual or mechanized using a double-cast BCV battery. An ALS system was also provided for multi-mold high-pressure casting of vitreous china items such as sinks, pedestals, cisterns, lids and squat toilets. In short, this nationally important project has set its sights on technologically advanced solutions capable of delivering high-quality products.
Completing the sanitaryware plant are high-efficiency Sacmi dryers and Gaiotto GA 2000 glazing robots: the latter are highly automated and feature state-of-the-art systems such as Mass Control® for supervising flow rates and optimizing glaze trajectories. The firing department, instead, has a high-performance, low-consumption Riedhammer kiln.
Technological know-how
On both the Tiles and Sanitaryware plants, the project extends well beyond the mere supply of machines: it also includes the tools and technological expertise needed to test body formulations, thus favoring the use of local raw materials. On the sanitaryware side, modelling solutions were also supplied and subsequently developed on-site during plant start-up, with an emphasis on elegant lines, an extensive color range and products with cutting-edge design.
The project was also an example of perfect coordination between the Italian parent company and the local network, headed by the Sacmi Istanbul hub: the latter provided the technical teams who managed all the delicate machine assembly and testing phases. The entire shipment was coordinated by Italiansped, a Sacmi company that leads the way in the logistics and international shipping fields.
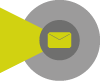
Did you find this article useful?
Join the CWW community to receive the most important news from the global ceramic industry every two weeks